Utilizzare fori ciechi nel PCB evitando criticità
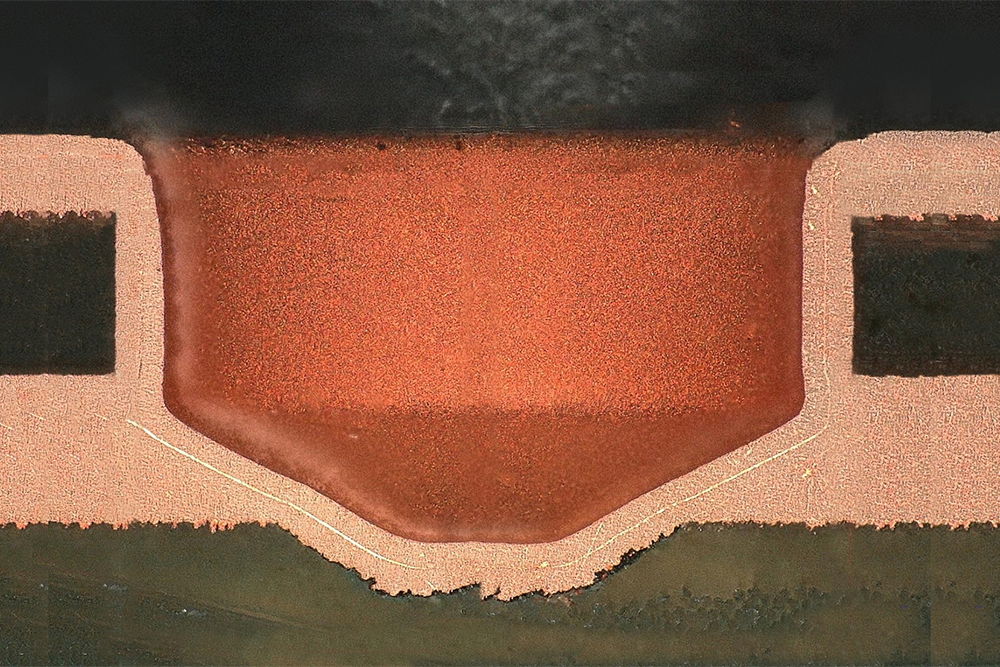
Guida all’impiego del blind via.
FORATURA CIECA E PARAMETRI COSTRUTTIVI
Per foratura cieca (blind via) si intende la realizzazione di un foro metallizzato che collega elettricamente uno strato esterno di un circuito stampato con uno interno, senza attraversare l’intero spessore del PCB.
Il foro viene ottenuto con una foratura controllata sull’asse Z e deve avere un diametro tale da garantire un ottimale riporto metallico sulle pareti.
Ci sono 5 parametri guida da considerare nella scelta del diametro corretto del foro cieco, in modo che garantisca qualità e affidabilità nel tempo
/5/ PARAMETRI DA CONSIDERARE NELL’IMPIEGO DEL FORO CIECO
Durante la progettazione del PCB per evitare criticità e avere garanzia di durata nel tempo:
1. Il diametro del foro.
2. La dimensione delle piazzole di rame connesse al foro cieco.
3. Lo spessore di isolamento fra i layers connessi dal foro cieco e lo spessore dei lati rame stessi.
4. La conseguente Aspect Ratio del foro.
5. Lo spessore di isolamento dal lato sottostante non connesso al foro (solo per i fori meccanici).
1 – DIAMETRO DEL FORO
Il foro può essere realizzato con lavorazione meccanica o laser:
FORO MECCANICO – esso può essere realizzato con un utensile di diametro minimo 0,15 mm (con tolleranza negativa ammessa di 50 µm) così di ottenere dopo la realizzazione dei riporti metallici al suo interno un foro di diametro di 0,05 mm (o qualche centesimo superiore).
FORO LASER – esso ha un diametro tipico di 0,1 mm all’atto della realizzazione (privo di tolleranza negativa) così di ottenere un foro di diametro a 0,05 mm (o qualche centesimo inferiore).
Nota: la metallizzazione di un foro cieco deve essere minimo 12 µm come previsto dallo standard IPC.
2- DIMENSIONE DELLE PIAZZOLE DI RAME CONNESSE AL FORO CIECO
La piazzola interessata dal foro cieco, per rispettare lo STD IPC e garantire così la produzione di un PCB ottimale, deve avere un diametro di dimensione almeno 300 µm (11.8mls) maggiore del diametro del foro cieco (considerando dei layers con spessore di rame di 35 µm).
Questo aspetto, per quanto banale, è molto importante per permettere una buona centratura del foro sulle piazzole stesse mantenendo la dimensione del foro richiesta. Per la foratura laser tale valore può essere ridotto a 250 µm (10 mls).
3- SPESSORE DI ISOLAMENTO FRA I 2 LAYER CONNESSI DAL FORO CIECO
Come per qualsiasi PCB gli spessori degli isolanti e dei layers conduttivi dipendono dalle esigenze di progettazione elettrica e ciò vale anche per i layers coinvolti nelle forature cieche. (collegato al Aspect Ratio)
4- ASPECT RATIO (AR)
L’ Aspect Ratio è il rapporto tra la profondità del foro cieco (data dallo spessore del dielettrico presente fra i 2 layers connessi dal foro, sommato allo spessore di rame dei layers stessi) e la dimensione del diametro del foro stesso.
La sua importanza deriva dai limiti chimico-fisici e fluidodinamici del processo elettrolitico di placcatura (metallizzazione) dei fori; nel processo di riporto galvanico diversi liquidi devono fluire in modo efficiente all’interno del cilindro ottenuto nel materiale di base dalla foratura (nonostante sia occluso da una parte) per ottenere un rivestimento metallico della parete del foro che sia robusto e con esso una connessione elettrica affidabile.
Detto rapporto deve essere al massimo di 1,4:1 calcolato considerando il diametro del foro a fine processo (cioè dopo aver realizzato l’apporto metallico all’interno del foro).
Ciò significa che nel costruire il build-up del pcb bisogna tener conto che lo spessore totale del materiale (dielettrico + lati rame coinvolti) attraversato dal foro dovrà essere solo poco superiore al diametro del foro atteso. In ottica inversa si dovrà dimensionare il diametro di fori e piazzole in conseguenza degli spessori di dielettrico e dei lati rame prescelti.
5- SPESSORE DI ISOLAMENTO SOTTOSTANTE IL FORO (solo per fori meccanici)
È lo spessore del dielettrico presente fra il secondo lato connesso al foro cieco e il lato interno a lui adiacente (sottostante) e non connesso. Date le tolleranze richieste dal processo di foratura controllata in asse Z e la forma dell’utensile utilizzato, tale spessore deve garantire il corretto isolamento elettrico a fine lavorazione.
ESEMPIO DI REALIZZAZIONE AFFIDABILE
su un pcb con lati rame di spessore 35um, ove il lato top e il primo lato interno sono isolati da 100um di materiale dielettrico e il secondo lato interno è a sua volta isolato da ulteriori 150um (E) di materiale, si può ingegnerizzare un foro cieco di diametro 150um (C) (non laser) centrato su piazzole circolari di diametro 450um (A). Tale foro viene realizzato con un utensile di diametro 250um (B), il quale, attraversando uno spessore di materiale (FR4 + lati rame) pari a 170um (D), porta ad un AR 1,13:1 (D/C), che essendo inferiore a 1,4:1 garantisce un’ottima realizzazione (lo spessore di materiale interessato dal foro cieco è appena maggiore del diametro del foro stesso).
Tabella esempi di minima realizzazione:
Altri post
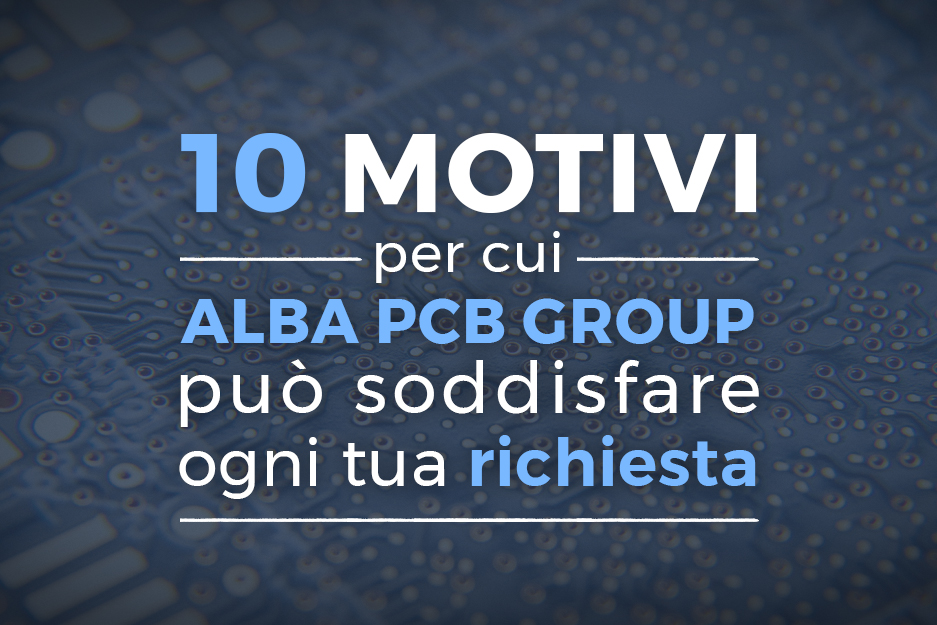
10 motivi per cui Alba PCB Group può soddisfare ogni tua richiesta
Alba PCB Group è un gruppo internazionale, con quartier generale in Italia, costituito da aziende...
Leggi tutto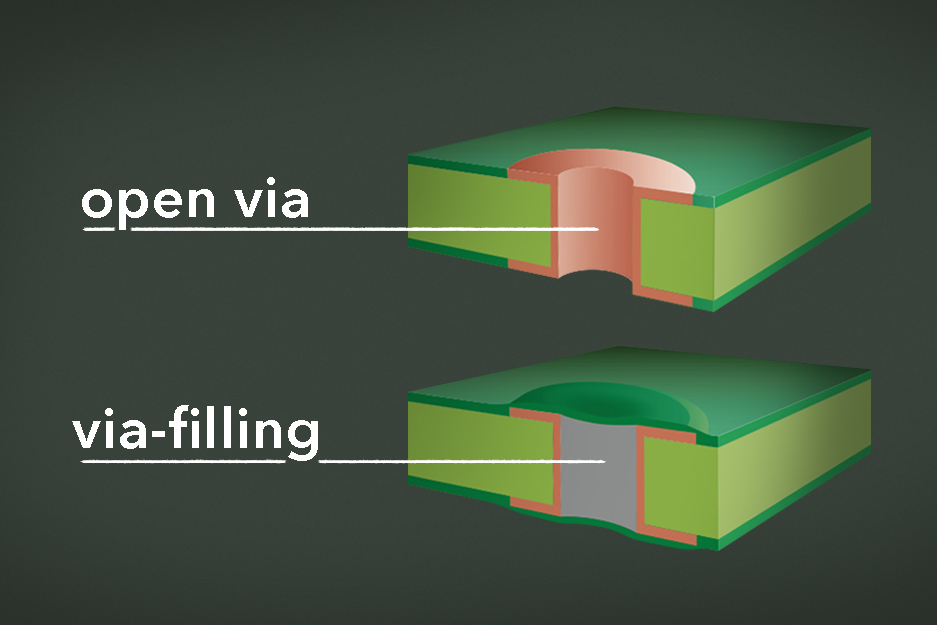
PCB: scegliere il tipo di VIA FILLING in base alle proprie esigenze
Quando si parla di Via Filling nei PCB si intende un processo di riempimento dei...
Leggi tutto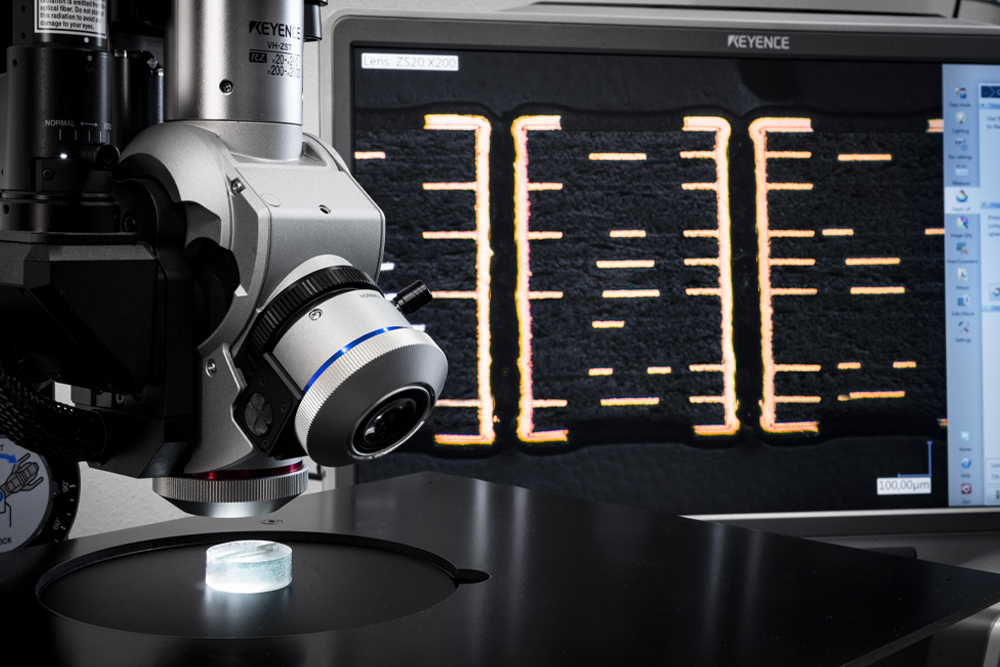
Controllare la qualità guardando “2000 volte” meglio!
Non stacchiamo mai gli occhi dalla qualità! Il nostro reparto di controllo del prodotto è...
Leggi tutto