Quality
We deliver safe PCBs
Verification of the customer’s project when it comes in
• DFM support on the product
• Automatic importation of files
• Feasibility analysis (Design Rule Check)
• Creation of a standard interchange format
• Drafting a management plan based on the product
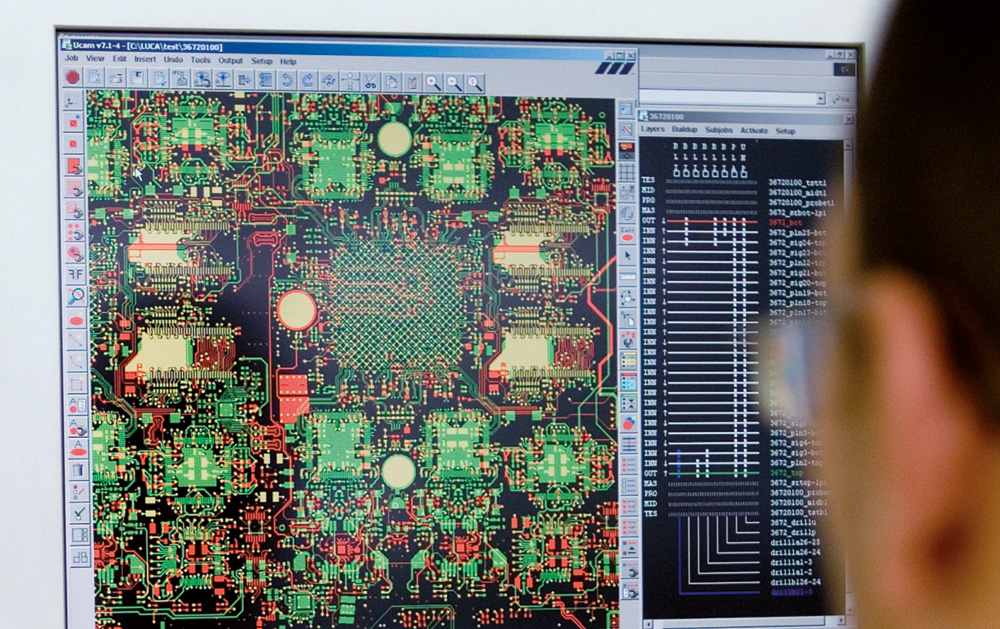
Checks of metal thickness
• Metal (copper) base thickness checks using specialised instrument (CMI)
• Finishing alloy composition checks with XRF instrument
• Finishing metal thickness checks with XRF instrument
• Metallographic test pieces (cross section)
• Non-destructive checks to measure the metallization thickness on holes using specialized instrument (XRF)
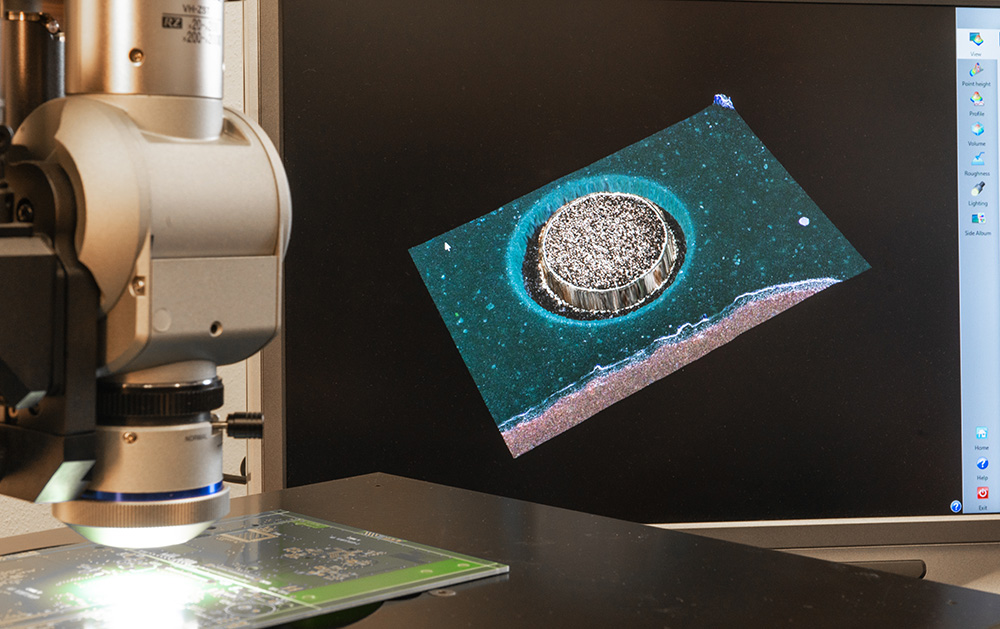
Mechanical Checks
• Dimension and mechanical checks using precision optical instrument (OGP)
• Micrometric depth controls for pre-cut V-cut (scoring)
• Mechanical processing controlled height controls using specialized instrument (OGP Z axis)
• 3D optical controls (Keyence VHX950F)
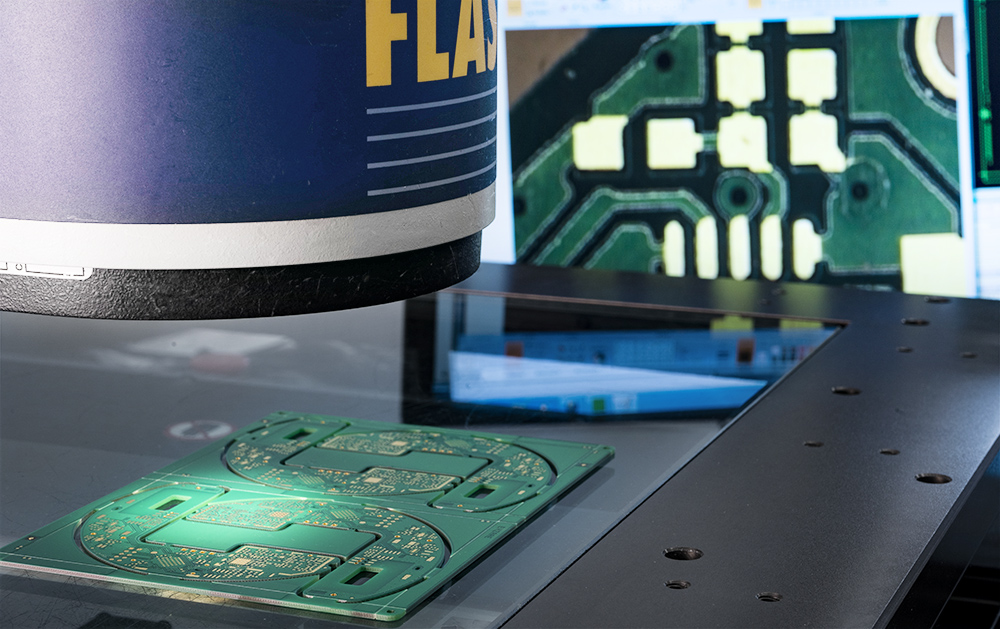
Other checks
• Verification of controller impedance lines (Z-metric ST300)
• Drill centring checks using X-Rays (INSPECTA)
• Ionic contamination checks (TIC)
• Wettability checks for finishings (Comparative Deep test and Wetting Balance Test)

First Article Report testing (FAR)
At the request of the customer, specific tests on the products can be performed on the first tooling production (new codes), so as to avoid possible anomalies that might then affect the success of mass production. Appropriate documentation is then issued.
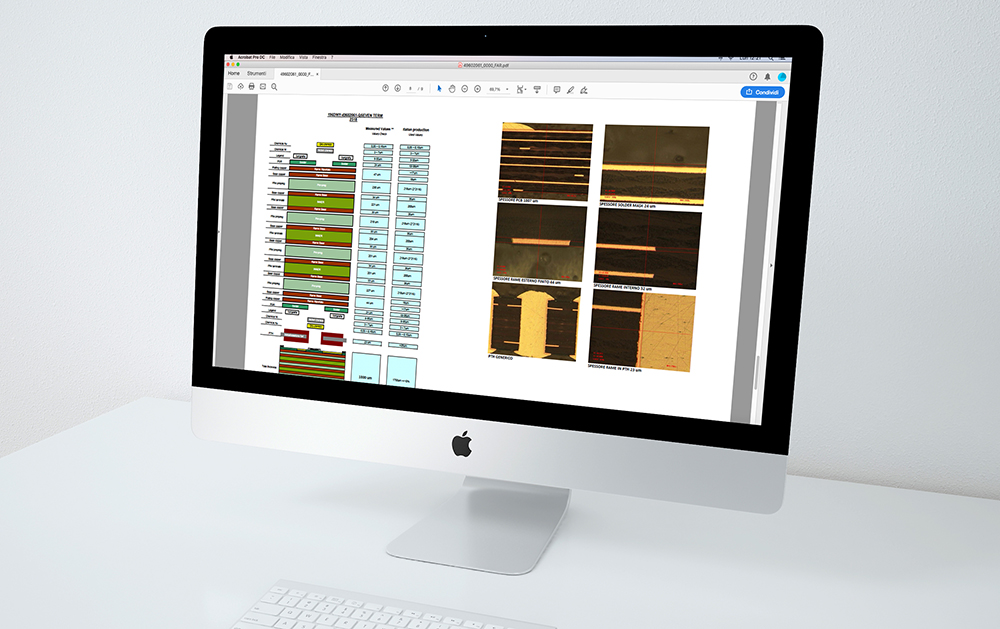
Production Parts Approval Process Testing (PPAP)
At the request of the customer, verification, registration, and approval procedures are performed for the production process of the circuit samples, which are numbered and filed individually. In this way the customer will have at his disposal a set of documents/reports (drawings, materials, processes) relating to the circuits built during the first sampling phase, which will be used as a comparison basis for subsequent mass productions.
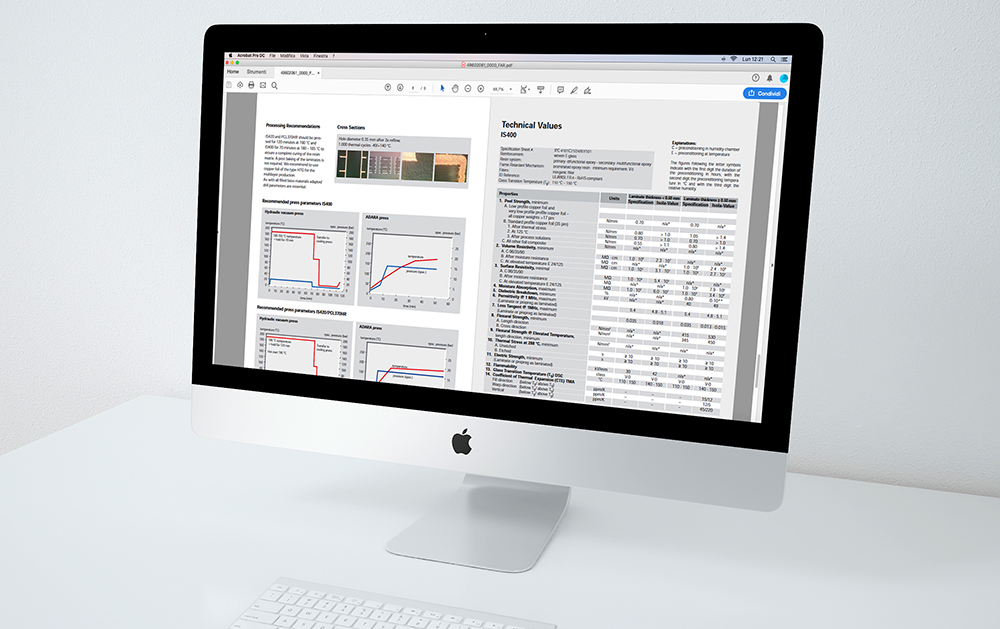